The concept of lean manufacturing is commonplace in the automotive industry. In this article we explore how Dearborn Mid-West Company (DMC), a manufacturer of automotive assembly lines, applied lean principles to their engineering processes.
Michigan’s Dearborn Mid-West Company is deeply intertwined with the auto industry. As a tier-1 supplier to Ford, Chrysler and GM, DMC designs the conveyor systems that transport hulking pieces of aluminum and steel as they are transformed into cars on assembly lines.
Traditional lean principles apply well to some of the automated, process-driven work DMC faces in manufacturing their assembly lines. However, they’ve also explored how to apply lean principles to product development processes that are typically not automated, such as engineering.
To create a leaner organization, the engineering leaders at DMC investigated the connections and workflows within the engineering processes. This can be a more complex process than it is in manufacturing due to the iterative nature of engineering, particularly in product development. One step is to eliminate wasted work, such as working on drawings that are out of date. This requires that everyone on the team work together from a common technology platform. Additional steps generally involve standardizing a single process of communication and then fine-tuning it to the point where it works reliably in multiple conditions.
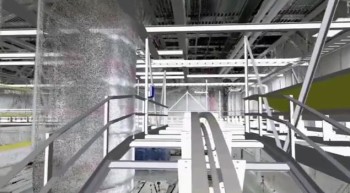
Another area to consider is wait times. There are many times when a model could go up the ladder for internal review or out to a customer. In between those times, the engineer is waiting. It’s hard to see the waiting because the engineer finds other activities to occupy their time, but the time loss is there nonetheless thanks to work disruption. One way that DMC has combatted this issue is by standardizing as many of the steps in the process as they can.
Over the long-term, the idea of eliminating waste can also apply to staffing levels and investments in tools for that staff. As you might imagine, during the lifecycle of an automotive line there can be a bit of downtime. Think about how long it takes for an automobile to be completely redesigned. Sometimes you’ll see the same body and chassis driving down the road year after year, with little changed except an upgraded navigation system or touch-to-text widget. That’s hardly the type of redesign that drives an infrastructure or assembly line change.
During that downtime does it make sense for DMC to keep a staff of CAD technicians and designers on high alert? Of course not. To ensure they have staff when they need it, however, DMC has developed a process to identify appropriate talent and integrate that expertise into their core team and tools—enabling a more rapid ramp-up when it’s time for action.
“We typically keep a small staff in house. However, we had a large conveyor system project that came in where we needed to staff up with five temporary workers for 6-9 months. Our Desktop Subscription for Autodesk Product Design Suite Premium was a lot less expensive than buying five extra full seats,” said Chris Hahn, Project Engineering Manager at Dearborn Mid-West Company. “It was quite a savings and we plan to repeat using Desktop Subscriptions to manage workload in the future.”
Applying lean concepts to engineering is a complex task, but as Dearborn Mid-West Company discovered the increased efficiencies are well worth the effort. To manage that complexity Dearborn focused on five key areas:
- Eliminating wasted work
- Defining common communication protocols
- Adopting a common technology platform
- Building core knowledge in a scalable small team and tools
- Scaling the team and tools to meet short-term bursts in demand